Through this article, understand the cause of the Clogging of the tundish nozzle and the method to solve the Clogging of the tundish nozzle. Understand the types of tundish nozzle Clogging and learn related product knowledge about the tundish nozzle. Welcome to visit our factory.
The Cause of Tundish Nozzle Clogging
The formation of accretions or clogging of tundish nozzles in the continuous casting of steel is detrimental both to caster productivity and to eventual inclusion content of the final product. The cause of the clogging is related to a combination of operating criteria including ladle slag practice, tundish refractory, deoxidation methodology and temperature.
To assess the effect of various slag components on clogging a mineralogical and rheological study was conducted on both plant and simulated accretion material. Minerals belonging to the lime-alumina-silica system such as hibonite, gehlenite, mullite, spinel and corundum, all having solidification temperatures at or above steelmaking temperatures, were most prevalent. In Mn-rich melts larnite, hibonite and a glassy phase were predominant. The rheological studies confirmed the formation of a significant solids fraction near steelmaking temperatures for basic melts whereas high (>30w/o) Mn melts were glassy. As well, the plate composition of the gating system was also deemed to contribute to the problem, with ZrO2 being preferable to Al2O3.
Designing tundish slags to minimise formation of refractory solids while maintaining reasonable compatibility with refractory and gating system practice.
Clogging of the tundish nozzle is a major castability problem in continuous casting of steel for several reasons.
Firstly, clogging increases the frequency of operation disruptions to change nozzles or tundishes or even to stop casting. These extra transitions increase operating cost, decrease productivity, and lower quality. Secondly, clogging can lead directly to a variety of quality problems. Clogs change the nozzle flow pattern and jet characteristics exiting the ports, which can disrupt flow in the mold, leading to surface defects in the steel product and even breakouts. Dislodged clogs also disturb the flow and either become trapped in the steel or change the flux composition, leading to defects in either case. Quality problems also arise from the mold level transients which occur as the flow control device compensates for the clogging.
Clogging is a complex problem which has received a great deal of past study. CX provides a summary of the formation mechanisms, detection methods, and prevention of tundish nozzle clogging.
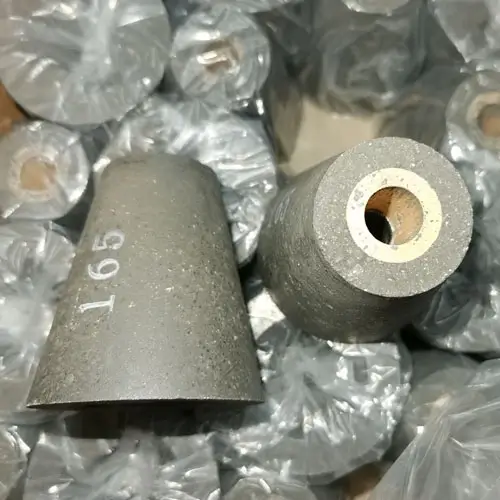
Types OF Tundish Nozzle Clogs
Tundish nozzle clogging problems take many different forms, and can occur anywhere inside the nozzle, including the upper well, bore, and ports. They are classified here into four different types according to their formation mechanism: the transport of oxides present in the steel to the nozzle wall, air aspiration into the nozzle, chemical reaction between the nozzle refractory and the steel, and steel solidified in the nozzle. In practice, a given nozzle clog is often a combination of two or more of these types, and its exact cause can be difficult to identify.
Transport of oxides present in the steel – The most important cause of nozzle clogging is the deposition of
solid inclusions already present in the steel entering the nozzle. These may arise from many sources:
(1) deoxidation products from steelmaking and refining processes
(2) reoxidation products from exposure of the molten steel to air
(3) slag entrapment
(4) exogenous inclusions from other sources
(5) chemical reactions such as the products of inclusion modification
Prevention of Tundish Nozzle Clogging
A score of different practices are helpful to minimize clogging. The remedies may be classified as inclusion prevention, inclusion modification (Ca treatment), nozzle material / design improvement, and argon injection.
1.Erosion of Alumina build-up
2.Steel reinforcement of Alumina matrix
3.Flow model studies
4.Argon purging facility in the bore of nozzles
5.Anti-clogging mix employment at bore
The best remedial action depends on the steel grade and exact cause of the specific clogging problem being considered.
What is a tundish nozzle?
Tundish Nozzles are an integral part of Continuous Steel Casting process. These products are instrumental in controlling the flow of Molten Steel from Tundish to Continuous Casting.
What are the uses of tundish?
What does a tundish do? A tundish is installed to prevent cross-contamination between an overflow pipe and a drain pipe. Unsanitary water from the drain pipe could theoretically enter the system if a tundish is not installed to block this.
What are the types of refractory nozzle?
The refractories for continuous casting are mainly classified into the following types: tundish refractories, flow control system refractories and teeming system refractories.
What is tundish nozzle made of?
Tundish Nozzles usually comprise a zirconia inner nozzle (often referred to as a “zirconia insert”) with a lower grade outer body such as Alumina, Zircon or Bauxite.
All in all, through this article, understand the cause of the blockage of the nozzle of the tundish and the method to solve the blockage of tundish nozzle. Welcome to visit the factory to learn more about refractory products and watch the process of producing refractory products.