Main damage factors of electric furnace refractory materials. By reading this article, understand the process of electric arc furnace and electric arc furnace operation. If you are interested in other EAF furnace refractory products, welcome to visit our factory.
In general, the main damage factors of EAF refractory are: erosion, oxidation, erosion, melting, stripping and hydration, among which oxidation and chemical erosion and erosion dominate.
1.Chemical erosion: chemical reaction between iron oxide (FeO) or acidic components in slag, such as SiO2 with CaO and MgO.
2.Oxidation: it is one of the main reasons for the corrosion of refractory materials in the lining of electric furnace. In the process, the carbon components in the refractory materials are oxidized by oxygen-containing components (such as iron oxide, oxygen and magnesium oxide), resulting in the material falling off and damaged.
3.Erosion or mechanical impact: physical damage is caused by the flow of molten steel or slag over the surface of the refractory material and physical wear or erosion of the furnace lining. Erosion at the outlet, slag line, electrode outlet or exhaust platform of the electric furnace is the most common. Peeling is a complex of recurrence of refractory damage mechanism, which is caused by the lining refractory suffered rapid heating and cooling stress caused by the refractory, the stress is often more than the strength of the refractory material, resulting in crack through the intersection and lining pieces will flake or fall off completely, this kind of circumstance commonly occurring on the furnace top.
4.Hydration: is a factor in the failure of electrical furnace refractories. In the process of use, it is easy to penetrate into the furnace cover or furnace wall, and water or water vapor can erode the lining of the refractories, in which magnesium oxide (or other basic oxides) reacts with water (or water vapor) and is hydrated.Requirements for the masonry BOF lining bricks.
The masonry quality of converter lining is the foundation of furnace life. Therefore, first of all, the quality of lining brick itself must conform to the standard; Then in strict accordance with the technical operation procedures masonry, to achieve the overall quality standard requirements.
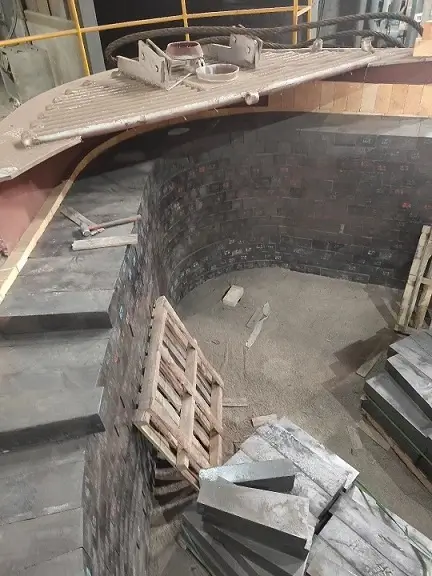
Electric Arc Furnace Process
The EAF is refractory lined and filled with scrap and/or other manufactured iron units. The scrap is melted with high-powered electric arcs from the node/nodes creating molten metal. High-quality refractory brick is required to withstand the high temperatures reducing heat loss to create liquid steel.
Modern EAF vessels have oxygen burners on the side to prevent cold spots in the melting scrap metal process. Once the melt is complete it is transferred into a ladle to start the next process.
Refractory Lining of the Electric Arc Furnace
Refractories for the lining of the EAF rely upon its design. The working circumstances additionally impact the refractory performance. The working conditions in the electric arc furnace call for refractories that are chemically fundamental and show a high level of resistance to high temperature as well as thermal cycling. The design of the contemporary EAFs highlights the capricious base tap-opening and calls for special refractories for their lining.
A large number of design features are associated with electric arc furnaces but their grouping is done based on the following:
1.Tapping design that includes bottom tapping or side tapping
2.The power source that includes DC (direct current), or AC (alternating current)
3.Supplementary oxygen (O2) use for an increase in the melting rate.
Part of the steelmaking electric furnace have the following performance requirements:
①Good chemical stability and volume stability:
②The material composition is not easy to react with molten steel and SiO₂, and it is not easy to produce nodules;
③It is not easy to be wetted and penetrated by molten steel;
④It has good resistance to rapid cooling and rapid heating, and is not easy to be damaged and peeled off;
⑤High density, low porosity, uniform distribution of pores, and impermeable molten steel;
⑥High strength, can resist the impact and erosion of mechanical external force.
Electric Arc Furnace Operation
The charging process to the furnace is in itself damaging to the refractory lining by both impact and the chilling effect of the cold scrap. The aggressivity to the refractory lining is further increased by rapid temperature increase during melting, combined with the attack by slag fluidizers such as fluorspar.
Preferential attack of the refractory lining occurs in the hot spot areas (opposite the electrodes) caused by flare, and at the slag line, owing to low basicity slags, and high FeO slags, often employed to aid phosphorous removal.
Slag balance and slag control can have a major influence on refractory wear, particularly control of MgO content by Dolomite additions to prevent dissolution of MgO from the lining.
Electric Arc Furnace Classification
EAF(Electric Arc Furnace) is mainly used for steelmaking industry, main raw material of which is scrap.According to power types, EAF are mainly divided into DC EAF and AC.
Same as other high temperature induction furnaces, refractory materials are widely used in EAF. EAF refractory materials are mainly as following,
1.DC EAF
Magnesia, magnesium carbon, magnesium aluminum and magnesium chrome refractories are widely used in DC EAF. Alkaline bricks without carbon is widely used in Europe, while in Japan, thermal shock resistance is thought as a great question, so they prefer to use magnesium carbon bricks with high carbon content. In order to improve thermal shock resistance and corrosion resistance of metallurgical equipment, magnesia spinel materials and magnesia-chrome brick are widely used in Europe.
2.AC EAF
For small AC EAF, asphalt brick, magnesium carbon brick, magnesia gun mix are widely used at furnace wall. For ultra-high power electric AC EAF, high-quality magnesium carbon brick would be used for furnace wall, while for slag line, higher performance high-magnesium carbon brick would be needed. Out of magnesia carbon bricks, magnesia gun mix would be used to repair furnace wall during working.
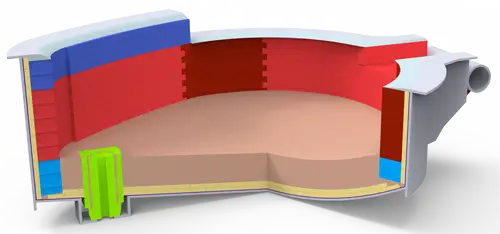
More details about Electric Arc Furnace
How does an EAF furnace work?
The EAF process uses electricity to melt scrap steel and other sources of metallic iron such as direct-reduced iron or hot metal, and additives are used to adjust the steel composition to the desired specifications. Casting, reheating and rolling processes are like those found in the BF-BOF route.
What is the advantage of EAF?
Steelmaking by means of EAFs is much more efficient in terms of the energy necessary for the process, since its operation requires mostly electricity, thus circumventing the consumption of a large portion of non-renewable resources.
What is EAF in steel industry?
Steel is principally made via two routes, the last Furnace-Basic Oxygen Furnace (BF-BOF) route and the Electric Arc Furnace route (EAF) – often referred to as the ‘primary’ and ‘secondary’ paths. The former is used to create new or ‘virgin’ steel, the latter is often used to recycle steel scrap.
In summary, this article describes the Main damage factors of electric furnace refractory materials. Learn more about electric arc furnace process and electric arc furnaces classification. If you are interested in electric arc furnace refractory products, please feel free to contact us!