Different refractory materials are suitable for smelting different metals or alloys. At present, medium frequency induction furnaces are widely used in metallurgy and foundry industries. During the use of induction furnaces, the impact, friction and electromagnetic stirring of the charge will aggravate the erosion of the furnace lining.
The factors that reduce the service life are:
(1) Operating conditions;
(2) Furnace construction and furnace baking process;
(3) Rationality of refractory raw materials;
Quartz sand refractory ramming material is widely used in the production of molten cast iron and cast iron alloys because of its high cost performance and good thermal shock stability, mechanical strength and acid slag corrosion resistance.
However, there are many types of quartz ores, and their important performance indicators such as impurity content and crystallinity are different, resulting in a large difference in the service life of quartz refractory materials on medium frequency furnaces.
In theory, quartz with low impurity content and high crystallinity has high mechanical strength and excellent thermal shock stability, and is particularly suitable as a lining material for large-capacity medium frequency furnaces, but the sintering performance of this quartz is poor, which will affect the service life of the lining.
Quartz ramming material is made of high-quality large-grained quartz sand as the main raw material, supplemented by a binder and a sintering promoter. During the production process, an important binder needs to be added. Boric acid is used as a sintering promoter. During the sintering process of the furnace lining, boric acid is dehydrated and converted into boric oxide. At high temperatures, boric oxide acts as a high-temperature binder and can promote the sintering of the workpiece.
In addition, when quartz ramming mass is used at high temperature, quartz will react with boric acid B2O3 to produce tridymite and cristobalite. Boric oxide can reduce the synthesis and sintering temperature of quartz without causing obvious harm to the material properties. Therefore, boric acid is an important raw material for quartz ramming mass.
The linear change rate of the ramming material after sintering increases with the increase of the content of the sintering agent boric acid. The linear change rate of the ramming material sintered at 1100℃ generally shows an increasing trend, and the linear change of the ramming material sintered at 1600℃ first increases and then decreases. It is worth noting that the linear change rate of the ramming material sintered at 1100 C is negative, because the sintering agent boric acid begins to form a liquid phase at this temperature, causing the sample to shrink; while the linear change rate of the ramming material sintered at 1600℃ is positive, and the sample expands. The reason is that quartz has a transformation from a low-temperature phase to a high-temperature phase at high temperature, accompanied by volume expansion. This phase change is irreversible, and the volume expansion still exists after the temperature is lowered.
A set of experiments show the important role of boric acid in quartz ramming material. The main raw material is quartz sand, whose critical particle size is 5mm. Different particle grading is carried out according to the maximum bulk density. At the same time, boric acid is added as a sintering agent. Then the test block is made in the furnace from 25℃ to 1500℃. The total weight loss of quartz is about 3.0; from 25℃ to 1000℃, the weight loss of quartz is about 2.2. This part of the loss mainly comes from the evaporation of free water and crystal water; due to the evaporation of free water, an endothermic peak appears at 80℃; due to the transformation of β-quartz to α-quartz, there is an endothermic peak at 580℃; due to the transformation of α-tridymite to α-quartz, a large endothermic peak appears at 1250℃. There are also thermal effects of other crystal transformations, but they are not very obvious, indicating that their phase changes are easier to occur.
The effect of the content of the sintering agent boric acid on the compressive strength of the ramming material. With the increase of the boric acid content, the compressive strength of the ramming material shows a significant increasing trend. From the B2O3-SiO2 phase diagram, it can be seen that after adding boric acid, a liquid phase appears in the ramming material at about 440°C, thereby promoting sintering and improving the strength of the ramming material; as the temperature rises, the amount of liquid phase increases, and the strength of the ramming material is bound to increase. However, due to the phase change of quartz at high temperature, the volume expansion accompanied by the phase change will partially offset the sintering effect of boric acid, making the influence of boric acid content on the strength of ramming material sintered at 1600°C relatively small. Boric acid mainly improves the medium-temperature sintering strength of the ramming material, while the role of the sintering promoter during high-temperature sintering is relatively small, and at this time it still mainly depends on quartz.
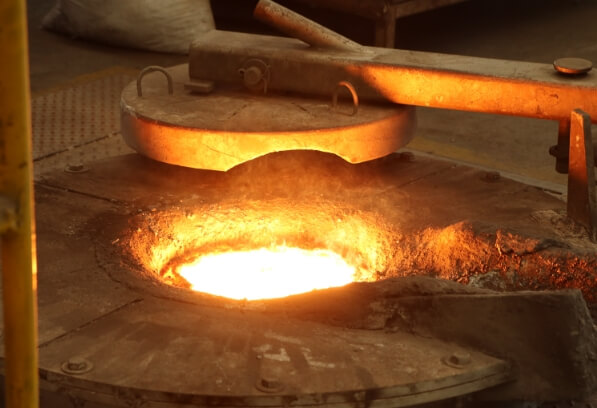