Electric arc furnace cover is an important part of the electric arc furnace lining, the length of life of the cover and its insulation performance is good or bad, on the steel production, quality, consumption and other technical and economic indicators have a very close relationship. Therefore, at home and abroad on the furnace cover has taken many measures, such as improving the cover material, improve the brick in the A1203 content, increase the bricklaying cover the arch and cover the center of the furnace cover to the height of the molten pool surface, improve the operation of the whole water-cooled cover, etc., and has achieved certain results. But still failed to solve the refractory cover of the use of short life, can not meet the electric arc furnace to large-capacity ultra-high-power development needs and the whole water-cooled furnace cover heat loss problem. For this reason, we try to use plasticized pounding material on the fully water-cooled cover of electric arc furnace, so that the advantages of full refractory cover and fully water-cooled cover are combined into one, and better results have been achieved.
1.Tamping material furnace cover production
Plasticity pounding material is made of special high alumina bauxite as the main raw material, plus part of corundum and stainless steel fibers, and aluminum phosphate as binding agent. Its main physical and chemical indexes are as follows: ω(A1203)=74.6%, ω(MgO)=9.50%, ω(Fe203)<1.70%, drying bulk density of 3.03g.cm-3, drying line change rate of 0.5%~1.0%, compressive strength>46.5 MPa, thermal shock stability (1100℃?) >25 times. water cooling)>25 times.
Firstly, mix the material well and trap the material for 1-2d, at the same time, weld the fixed hooks made of rebar evenly on the inner feeding surface of the whole water-cooled furnace cover, and then mix the material for the second time, and use the special tool to mash the plastic which has been stirred and mixed well on the inner side of the whole water-cooled furnace cover. Wet or dry pounding. After pounding, the cover is put in a ventilated dry place to dry naturally for one week, and then it is baked in a dry kiln for 1-2d at low or medium temperature, and then baked at high temperature, so as to achieve the purpose of removing moisture and preheating in the pounded material.
In order to avoid water leakage during the use of pounding material furnace cover, before pounding plastic, the full water-cooled furnace cover should be tested for pressure resistance, and 0.6 MPa water pressure is routinely used to test whether the water-cooled pipe is leaking or not; when baking at high temperature, the water-cooled pipe must be filled with water to avoid uneven stress at high temperature, which will destroy the weld seam and the tension bar and lead to leakage of water in the process of its use.
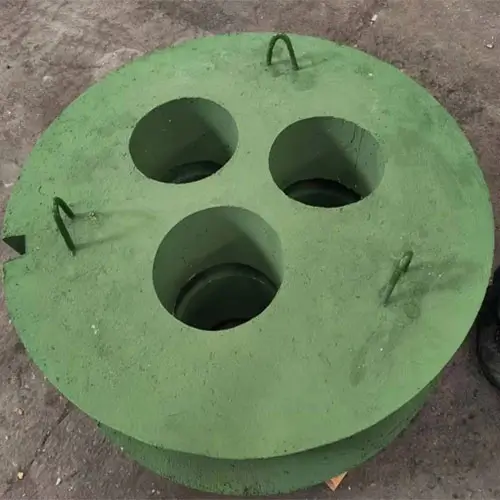
2.Application and analysis
Use conditions: electric arc furnace output 17t; furnace shell diameter 3700mm; transformer capacity 5500kVA; secondary side current 12210A; secondary voltage 260-139V, divided into 6 gears; to produce 20 billet steel, manganese steel.
A total of 8 malleable pounding material furnace covers were made for this test, among which 1#-4# covers were dry pounding and 5#-8# covers were wet pounding.
Through data comparison, the more plastic pounding, the thicker the pounding layer, the longer the service life of the furnace cover, the better the heat preservation performance, the more obvious the effect of reducing power consumption and so on. Therefore, in the case that the load capacity of the lid lifting mechanism allows, the plastic pounding layer should be as thick as possible. At the same time can also be seen, in the pounding of plastic dosage is basically the same case, the service life of the cover is also a big difference. This is mainly related to the amount of water added to the construction of the plastic, pounding quality, natural drying time and baking quality.
In the process of use, it is found that: in the case of the amount of water added to the construction of plastic and the quality of pounding are basically the same, the natural drying time is long, the baking quality is good, and the service life of the stove cover is longer; if the temperature of the stove cover rises too quickly when baking, the pounding layer will be delaminated in the process of baking; if the temperature of the baking is not up to the requirements, the pounding layer’s resistance to thermal shock is poor, and it will delaminate and detach in the process of use. Therefore, after the inner side of the fully water-cooled furnace cover is pounded on the plastic, the natural drying time should be ensured (especially for the wet pounding cover), and the baking time in low, medium and high temperatures should be controlled, and it is strictly forbidden to raise the temperature too sharply, so as to remove as much as possible the moisture in the pounding layer, prevent bursting and improve the service life.
With the use of plastic pounding on the inside of the fully water-cooled furnace cover, the smelting power consumption of tons of steel can be reduced by at least 69kW/h. Removing the cost of plastic pounding material (including labor costs), the cost of tons of steel is reduced by 28.25 yuan. Trial process also found that not only smelting power consumption is significantly reduced, but also due to the good insulation performance of the furnace cover, the smelting process is warmed up quickly, slag fast, good reducing atmosphere, white slag to maintain a long period of time, the smelting time is short, and is of great significance to improve the quality of steel.
The use of plasticized tamping material on the fully water-cooled furnace cover of electric arc furnace has better solved the problems of large heat loss of the fully water-cooled furnace cover and low service life of the fully refractory furnace cover, and has achieved good results. It not only improves the service life of the cover, reduces the smelting power consumption, shortens the smelting time, reduces the cost of tons of steel, but also heats up quickly during the smelting process, slag fast, good reducing atmosphere, white slag keeping time is long, the smelting time is short, and improves the quality of steel.
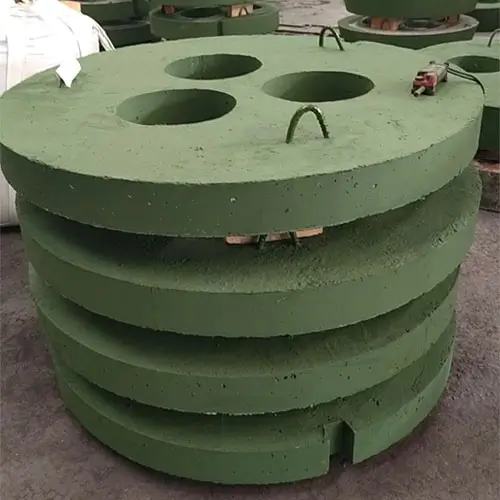