In modern iron and steel metallurgical production, the ladle plays a vital role as a key equipment connecting the steelmaking furnace and the continuous casting machine. It is not only used to store and transport high-temperature molten metal, but also an important place for molten steel refining, composition adjustment and temperature control. However, the working environment of the ladle is extremely harsh. It needs to withstand high temperatures of more than 1600℃, severe thermal shock, and erosion by slag and molten steel. Therefore, choosing the right refractory material becomes the key to ensure the safe and stable operation of the ladle.
The refractory material for the ladle must have a series of special properties. First, it needs to have extremely high refractoriness and be able to withstand direct contact with high-temperature molten metal. Secondly, good thermal shock stability is essential to cope with frequent temperature changes. In addition, the refractory material must also have excellent anti-erosion properties and be able to resist chemical erosion by slag and molten steel. Permeability and cost-effectiveness are also important considerations.
However, even if high-performance refractory materials are selected, the ladle lining still faces serious erosion problems. Studies have shown that the erosion of refractory materials mainly occurs at the interface between slag and refractory materials. When the Al2O3 content in the slag is high, a high melting point isolation layer will be formed at the interface, thereby improving the corrosion resistance of the refractory. However, when the Al2O3 content is too low, it will promote the formation of a low melting point phase and accelerate the erosion of the refractory. This complex erosion mechanism poses a huge challenge to the design of refractory materials.
To solve this problem, researchers are exploring a variety of innovative methods. One effective strategy is to introduce specific components, such as calcium hexaaluminate (CaO·6Al2O3, CA6) or nanomaterials into the refractory matrix to adjust the composition and structure of the material. For example, Dong Jianxiong et al. successfully improved the density of the refractory by introducing calcium hexaaluminate into the corundum matrix, and increased the slag viscosity by consuming CaO in the slag, effectively preventing the penetration of the slag.
Another innovative method is to use surface coating technology. By forming a protective coating on the surface of the refractory, the erosion of the refractory by slag and molten steel can be effectively blocked. This technology can not only increase the service life of the refractory, but also improve the purity of the molten steel and reduce the generation of non-metallic inclusions.
With the advancement of science and technology, researchers have begun to use advanced technologies such as big data and machine learning to deeply study the erosion mechanism of refractory materials. By establishing a multi-scale, multi-field coupled numerical model of the “slag-metal-refractory” ternary interface, the erosion behavior of the refractory can be more accurately predicted, providing strong support for the research and development of new refractory materials.
Looking ahead, the development of new refractory materials suitable for ultra-low oxygen steel (or clean steel) smelting will become a research hotspot. These new materials should not only have excellent thermomechanical properties, but also have the function of purifying molten steel and effectively remove non-metallic inclusions in molten steel. By rationally selecting refractory raw material components and optimizing structural design, researchers are expected to achieve precise control of refractory performance, thereby further improving the service life of the ladle and steelmaking efficiency.
The research and development of refractory materials is not only related to the efficiency and quality of steel production, but also the key to promoting the entire metallurgical industry to a cleaner and more efficient direction. With the continuous emergence of new materials and new processes, we have reason to believe that future ladle refractory materials will make greater contributions to the sustainable development of the steel industry.
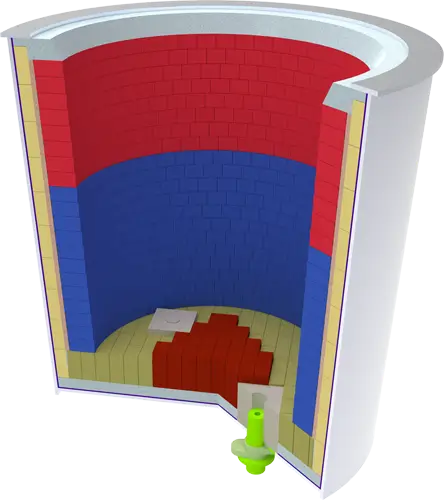
What is ladle furnace slag used for?
It is generally used in construction materials, soil rejuvenation, and CO2 capture. This paper reviews the production process, the mineralogical and morphological properties, stabilization techniques, and the applications of ladle furnace (LF) slag.
What is the difference between ladle furnace and electric arc furnace?
While the ladle furnace’s function improves the quality of the molten steel, the electric arc furnace process, on the other hand, is aimed at the raw material’s first melting. In unison, these technologies allow the required quality steel to be produced that is suitable for many applications.
What is an LRF furnace?
A ladle refining furnace has the ability to reheat the liquid steel. This allows the steel-makers to add greater amounts of alloys to the liquid steel.
What is the LF process of steel?
LF Ladle furnace steelmaking process is to put the molten steel in the final stage of oxidation in the converter or electric furnace, pour it into the LF furnace, remove 50-90% of the oxidized slag, and add reducing slag and deoxidizer for reduction refining.